News
The following is an Australian Dirt Bike Tech Feature article on CYLINDER ELECTROPLATING
FAR FROM BORING
The days of cylinder boring are slowly fading away, and the changing of the guard is now represented by a handful of small scale Nikasil cylinder reconditioners. We spoke to one of Australia's leading specialists in the field, LM Electroplating, about the technical process, why they reconditioned cylinders and what's in it for you.
The worst sound a rider can hear is the unmistakable destruction of a top-end. When a circlip decides to take a wander into the busy world of moving piston and stationary cylinder, most would say it's definitely all over for your $800 cylinder. What most bike owners don't realise is that when they look at a hole or score midway up the cylinder, it's not necessarily time to toss it in the recycling bin.
We'd heard round the traps that there was a way to sidestep the $800 cylinder replacement cost with a half price alternative. Immediately we had to wonder about quality. But we'd also heard that the Kawasaki�race team used this mob for the recoating of even their stock cylinders. We know plenty about overseas cylinder reconditions, but nothing about those that operate locally. We just had to send the ADB tech inspectors for a snoop into the silent cylinder closet.
A full day at LM Electoplating Industries, and we were dumb struck that no one had really uncovered some of the great stuff these guys do. Rob and Larry Houghton from LM have delved deep into the mystery of cylinders, and now sell the product of their own process, Electrosil, as a viable means of recoating and reconditioning stuffed cylinders for around half the price of a new unit. The quality of finish is outstanding, as illustrated by the backing of Kawasaki, and the process it local. We were starting to like them already.
Cylinders
Firstly, let's take a look at the two main sorts of cylinders so we can better understand the sort of work that Rob and Larry from LM do. All cylinders are mostly aluminium but this material is too soft for contact with steel piston rings. This means that all cylinders need a liner. Bike cylinders come in tow main sorts - ones with boreable cast iron liners and ones with Nikasil liners. LM Electroplating work only with Nikasil cylinders because that's what performs best and is most popular.
Nikasil Coatings
The Nikasil coating is essential, and must stay intact to keep your engine going. Any little scratches and the coating will be stuffed and the top-end won't last much longer than a sprocket with one tooth left on it.
The cylinder coatings from each manufacturer are generally referred to as Nikasil, but vary markedly in the actual composition of the Nikasil. Nikasil is an abbreviation for a Nickel and Silicon Carbide composite, which usually runs at about a 14 per cent Silicon Carbide ratio. Nikasil is a lot like concrete in that the Silicon Carbide acts as the sand and gravel, while the Nickel acts as the cement. The composite form a matrix, which binds very tightly and provides the strong surface required to withstand the force of a slapping piston. The Silicon Carbide particles stand as little peaks on a microscopic level, while the Nickel holds the peaks together. The two-stroke lube, or the engine oil on four-strokes, sits between these peaks to form a lubricating surface which allows the piston to move easily at high speed.
LM Electroplating Industries have their own stuff called Electrosil. Electrosil is the same as Nikasil, except that LM's Electrosil is its own blend of Nickel, Silicon Carbide and select additives. LM have taken four years to develop Electrosil through extensive R & D and surface studies.
When does your cylinder need recoating?
When you've seized�your bike, broken a piston or ring (both will scratch your cylinder lining), or just worn through the Nikasil, you'll need to either replace or recondition your damaged cylinder. LM recondition cylinders to standards as good as, if not better than, stock. They can also fill holes in the cylinder wall, take bores back to round after being oval, and then recoat the cylinder with their own product, called Electrosil. According to LM, motorcycle manufacturers have cut down Nikasil coating thickness to the bare minimum, and sometimes below. Also, Kawasaki use a process to coat their cylinders called electrofusion. This process is far less accurate and more likely to give trouble. The Kawasaki race team ports and then gets their stock cylinders recoated by LM before they even use them. For serious race turners, LM also recommend that stock top-ends on all bikes are stripped and blueprinted to remove any small burrs or debris from assembly. In the meantime though, inspect your cylinder liner next time you tear down the top-end for any dull spots or scratches. pay particular attention to the exhaust port area, as this part of the cylinder cops most flak.
The Process
Here's what LM do to the cylinder from when it arrives in a couriered box till when your screaming in the phone a day later so you can get it back for the next "big race". For future reference, turnaround time is approximately 10 to 14 days (Editor: now 3-4 working days).

So you've just wrecked it. You've got your scored, holed and scratched cylinder and you want it fixed. You give it a tub, remove all studs and powervalves, and send it off to LM. LM use a multi-stage cleaning process which actually strips all grease and dirt, and even the old Nikasil from the cylinder. If the powervalves were left in, they would be melted out too. Note on this cylinder the shiny bits around the ports. This is stuffed because the piston has worn though the coating and actually scrubbed a bit of itself onto the cylinder.

What's left after the cleaning process is just the cast aluminium cylinders, which Rob and Larry call a blank. This is a Husky cylinder which is about to be checked for irregularities in the bore.
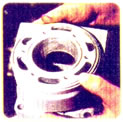
The blank is given a light hone on their customised plateau honing bar (definitely not any old ball hone). This reveals any high spots. Usually when a bike seizes, the position will scoop a bit out of the cylinder. This cannot be plated over. The blank cylinder has to be perfectly round, and the right size to match the piston (which has to be supplied when you give your cylinder to LM). If there are high spots, the blank cylinder is bored back to round, and square to the base of the cylinder. This is a KTM cylinder with a big low spot about the exhaust port.

Any porting or welding is also done at this stage to the cylinder blank. This is where LM also bore cylinders to match big bore pistons. Before the next stage of the process, the cylinder is crack-tested with an acid solution. Once all this is done, the cylinder is ready for replating.
LM's Electrosil is deposited on the aluminium blank with a dipping and plating process called electroplating. We weren't allowed to take photos of this top secret section of the process so we'll have to sue a few words. The cylinder is given a positive charge, while an Electrosil rod is negative in a vat of salty solution. Positive attracts negative, and so the material flows from the Electrosil rod onto the cylinder. The Electrosil is deposited on the bore at a constant rate, so that the longer the cylinder is dipped for, the thicker the coating. That means LM can coat their cylinder to custom thickness to give greater longevity or to compensate for when the cylinder is bored to straighten an oval or warped shape. LM have devised a way similar to that of Yamaha, Honda, Suzuki, Husky, KTM, and Honda (Kawasaki use a different process), whereby they mask the cylinder so the electroplating only occurs on the cylinder bore, and overlaps just slightly into the port areas. To plate the whole cylinder would be a huge waste of material, the stud holes would be ruined, and the powervalves wouldn't fit in the cylinder any more. The actual electroplating process is highly secretive because cylinder manufacturers and LM don't want to give away how they mask everything except the cylinder's bore. Also, the Silicon Carbide to Nickel ration and additive selection is kept a secret.

Once the cylinder is plated, it is given a light hone on the plateau hone and measured to see the coating thickness fits the piston perfectly.
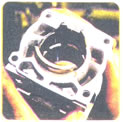
LM time the dipping process perfectly so that the cylinder usually comes out with exactly the right thickness of coating. Note how the plating laps over into the ports just slightly. Also, the bore is left perfectly smooth and shiny. Your cylinder is ready to race.
Nikasil - the common mistakes
Many bike owners and even bike shops take to ports with a grinder in an attempt to scavenge horsepower from their stock cylinders. Porting is carried out almost everywhere the wrong way - in a way that leads to a stuffed cylinder. In stock form and after Electrosil have recoated a cylinder, the Nikasil coating is "keyed in", or wrapped around the port edges, to give the rings a perfect seal as they travel up and down. Most porting cuts the coating around these edges where the bore feeds into the ports. This breaks the critical Nikasil coating around the port edges, and will always lead to flaking of the Nikasil. It won't take long before the cylinder has to be recoated. The lesson is that porting should only be done if the cylinder is going to be recoated immediately.
Also, may mechanics use a ball hone on cylinders before reassembling during a top-end rebuild. Ball hones are used to create fine oil retention paths on cast iron cylinders. On Nikasil cylinders, however, a ball hone won't do this. Instead, a ball hone will knock the Silicon Carbide peaks from the coating which wrecks the surface's oil retention capability. Ball hones are a bad idea for use on Nikasil coatings. LM use a special plateau hone, which they developed specifically for Electrosil. The main reason they use the hone is to aid with ring run-in more than oil retention. Nikasil cylinders should be cleaned but not ball-honed before reassembly.
How are LM better than the rest?
LM only do 40 cylinders a week. They do not batch-coat cylinders, like all the major cylinder manufacturers, preferring to work with each cylinder to get the most precise thickness in the coating and a better match to the piston. This is one of the points that LM prides itself on. Its cylinders are coated to within a two micron tolerance, which is five times more accurate than stock. This means the piston will fit better in the cylinder at operating temperature and cock less in the bore as it goes up and down which will increase the life of the cylinder. LM's coatings are thicker than on any stock cylinder, which means that the cylinder will last longer. The coating can be laid up to half a mil thick and is at least two thou thicker than any stock coating. Also, LM's Electrosil and electroplating process have taken eight years to develop to their stringent standards.